For right now, a nice pile of parts....
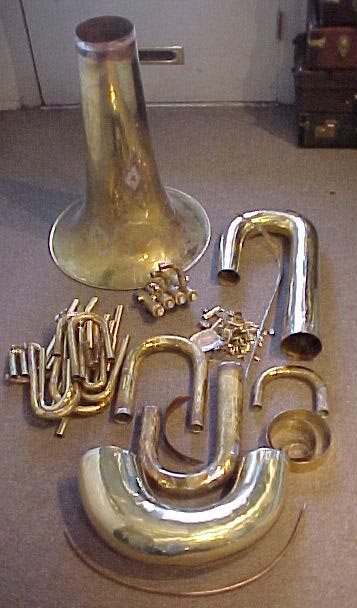
You mean this hole?harold wrote:Dave,
I saw your horn yesterday and Dan pulled the patch off of the back side of the lower bow.
There is a hole there big enough to push a nickel through - truly an impressive hole.
He is going to do an inlay on it and then have it coppered and sanded a few times to build up the material and to smooth out the surface.
harold wrote:He also told me the plan is to make some bow caps for it as well.
I'm certain that it is going to be an impressive bill once he gets done, but you are going to have an incredible instrument - you lucky dog!
Dan just sent the photos of the repair of the above hole. First he reshaped the bow and removed all the dents, then brazed up the cracks. Then:Bandmaster wrote:You mean this hole?
Actually, you can start over, just get two 24''x18'' sheets of 22 gage brass, your best and largest metal forming hammers, torch, etc. and make a new bottom bow.-- Unlike my curly-que piece that I made for the 5th valve tubing on my helicon, you couldn't simply "start over" if you had really screwed up that patch-in braze repair.
Webster got it basically right: to heat and then cool (as steel or glass) usually for softening and making less brittle; also : to cool slowly usually in a furnace.harold wrote:What exactly does this mean? Is there an industry standard definition of annealing? How long does it take and how do you know when you are done?-anneal bow entirely (dead soft)
Dan is right--I didn't read his description carefully enough. I was explaining why he would anneal the brazing, not that it necessarily needed to be annealed. Annealing is always done to remove the work hardening so that the material is no longer brittle and can be worked more without cracking. Welds are often annealed to soften the material uniformly through the patch, but quenching the weld itself would probably accomplish that (I was thinking steel and aluminum where you don't quench after welding or annealing).harold wrote:Dan says that he annealed it BEFORE putting the patch in place and Rick is suggesting that it needs to be annealed AFTER the patch was braised into place.
...
What is "fire scale"? Where does it come from? is it a byproduct of the heat and the brass? Aren't you loosing material (i.e. brass) in this fire scale?
This is what Dan calls "pickling". If I remember right, the acid solution is hydrochloric acid diluted in water. But I am not sure what concentration he makes it.Daniel C. Oberloh wrote:After allowing it to air cool for a minute or so, it is finally quenched in an acid solution to remove fire scale that forms on the surface of the metal during the annealing process.